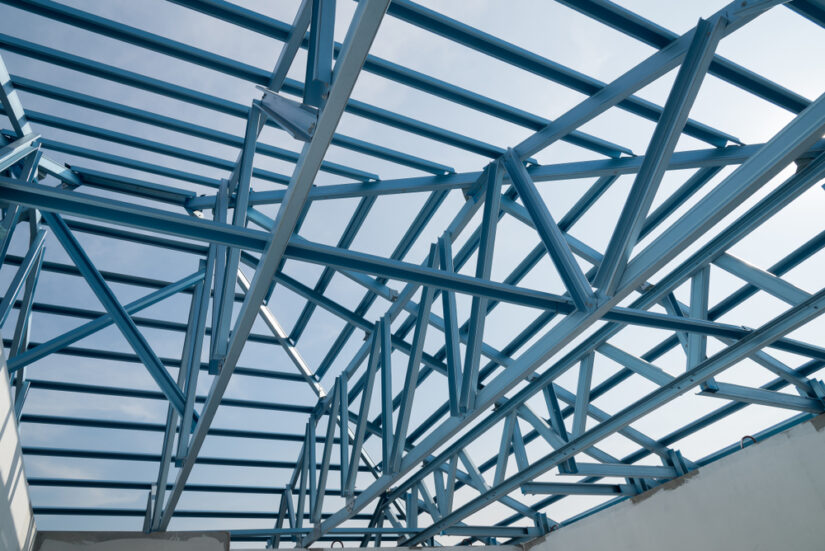
A 40×60 metal building is a versatile structure commonly used for agricultural, commercial, or industrial purposes, as well as for workshops or airplane hangars. The cost of such a building can vary widely based on factors like the price of steel, the complexity of the design, and the level of customization desired.
Steel prices fluctuate due to market conditions, which directly affect the cost of a metal building. The basic shell of a 40×60 metal building may start at an approximate cost of $20,000, but this figure can increase significantly with interior finishes, insulation, doors, windows, and other features.
When considering the purchase of a 40×60 metal building, buyers must also take into account additional costs such as foundation work, assembly, and potential shipping charges. These factors can contribute to the overall cost, making it important for individuals and businesses to obtain comprehensive quotes from manufacturers and contractors to budget properly for their projects. Geopolitical events and other global factors impact steel commodity prices. (Explore current and historical rates here.)
Understanding 40×60 Metal Building Costs
When considering a 40×60 metal building, understanding the cost factors is essential. The common size for a metal building of this type provides 2,400 square feet of space, suitable for various applications such as workshops, garages, or storage facilities. The total cost of a 40×60 steel building can vary significantly, influenced by design complexity, materials, and customization level. Check out our Steel Building Services for more information.
Base Costs
The base price for a pre-engineered 40×60 metal building kit might range between $7.50 and $8.50 per square foot. This equates to an estimated cost of $18,000 to $20,400 just for the kit, excluding additional expenses.
Design & Customization
Costs escalate as you customize the design. Choices related to doors, windows, and insulation impact the final price. For instance, opting for high-grade insulation or premium doors can increase costs.
Additional Costs:
It’s vital to consider additional costs beyond the base kit:
- Foundation: Concrete slab costs can range from $4 to $8 per square foot.
- Assembly: Erecting the building may cost an additional $3 to $5 per square foot if hiring contractors.
- Finishing: Interior finishes, utilities, and exterior touch-ups will add to the total cost.
Site preparation, permits, and indirect costs such as delivery should also be factored into the budget.
In conclusion, a 40×60 metal building is a significant investment and before making any decision, check for metal building different examples. Potential buyers need to account for all these variables to get a clear picture of the final cost. Prospective owners are encouraged to seek detailed quotes from manufacturers and contractors to outline a realistic budget for their projects.
Factors Influencing Cost
Foundational Requirements
The choice of foundation plays a critical part in determining the overall cost. Concrete slabs are commonly employed due to their durability and support. The concrete slab cost hinges on the thickness and reinforcement needed, which depends on the building’s purpose. For instance, heavy machinery necessitates a thicker slab compared to storage use.
Customization and Accessories
Customizations and accessories enhance functionality and aesthetics but also drive up the price. This includes selecting specific roof styles, adding insulation for temperature control, and incorporating ventilation systems. The addition of doors and windows also contributes to the cost, and their sizes and quantities should be factored in.
Location and Climate Considerations
Finally, the location and climate significantly impact costs. Transportation fees to remote areas can increase expenses. Moreover, buildings in areas with severe weather may require extra reinforcement. These might include robust anchoring for high wind resistance or a heftier roof style to support heavy snowfall, both of which affect the final price tag.
Costs of Construction and Installation
Labor Expenses
Labor costs form a substantial portion of the overall construction budget. They are affected by various factors, such as regional wage rates, complexity of the construction, and time frame for completion. On average, labor can amount to about $3 to $10 per square foot. This means for a 40×60 metal building, which equates to 2400 square feet, labor costs could fall between $7,200 to $24,000.
- Skilled labor: Generally more costly due to specialized skills.
- Unskilled labor: Less expensive but essential for completing simpler tasks during construction.
- Overtime: May increase costs if the project requires accelerated timelines.
Site Preparation and Materials Delivery
Before construction can commence, the building site must be adequately prepared. This includes grading, which ensures level ground, and can cost $1.50 to $2.50 per square foot depending on the topography and soil conditions. Thus, site preparation for a 40×60 building could range from $3,600 to $6,000.
Materials delivery is another critical factor with costs that vary based on proximity to suppliers and the volume of materials. Notably:
- Proximity to supplier: Closer distances can reduce delivery costs.
- Delivery logistics: Costs increase with the complexity of the delivery, such as the need for special transportation methods.
The installation involves the assembly of the metal building components on-site. This process includes the erection of the frame, placing metal panels, and securing the building to the foundation. Installation costs are often included in the quoted labor costs but can also be calculated separately based on the scope of the project.
By attending carefully to labor and site preparation costs during the planning phase, project managers can ensure more accurate budgeting for the construction and installation of a 40×60 metal building.
Maximizing Your Investment
When investing in a 40×60 metal building, one’s focus on long-term benefits is crucial, considering aspects like durability, which affects maintenance costs, and the financial approach, which provides potential cost savings.
Durability and Maintenance
Metal buildings are revered for their durability and low maintenance requirements. A 40×60 metal building typically comes with a structural warranty, ensuring it withstands various environmental conditions without the need for constant repairs. Maintenance involves periodic checks and basic cleaning, which helps in keeping the longevity of the building high and the costs low.
- Warranty: includes structural aspects with varied terms.
- Maintenance Checklist:
- Roof inspection
- Gutter cleaning
- Paint touch-up (covered by paint warranty)
Financing and Cost Savings
Exploring financing options is integral in maximizing investment in a metal building. Various lenders offer specific programs for construction and real estate, which can lead to significant cost savings over the term of the loan.
- Financing: loans, mortgages, or lease-to-own options.
- Cost Saving Strategies:
- Comparative lender shopping
- Early loan repayment plans
For example, if you want to purchase and install a budget-friendly 40 x 60 steel building kit, we suggest reaching out to our skilled US Patriot Steel building team for precise pricing and expert assistance throughout the buying and setup phases.