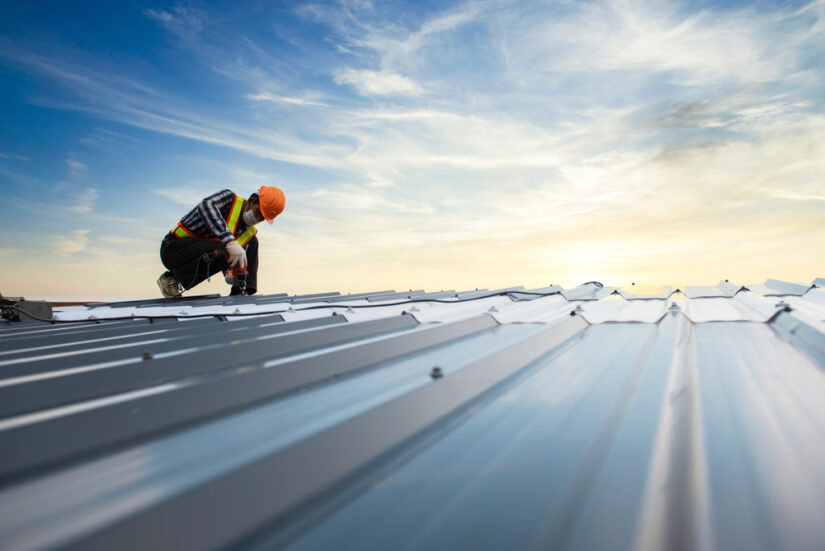
The cost of a 12×24 metal building can vary significantly based on a number of factors including materials, customization, location, and the complexity of the design. Metal buildings of this size are popular due to their versatility, serving a wide range of uses from storage sheds to workshops to small garages. The price for a basic model often starts in the low thousands but can increase substantially with added features and customizations.
Material quality and the price of steel play a critical role in determining the overall cost. Standard gauge steel that suits most applications is generally more affordable, whereas thicker, higher-grade steel for heavy-duty purposes will increase the cost. Additionally, prices fluctuate with the steel market, which can affect the final price even during the planning phase.
Understanding Metal Building Costs
Factors Influencing Cost
The cost of a metal building varies widely based on several key factors:
- Materials: Steel prices fluctuate due to market conditions.
- Size: Cost is typically calculated per square foot; a 12×24 structure is 288 square feet.
- Customization: Options like additional doors, insulation, and color choices affect costs.
- Labor Costs: These depend on the complexity of the project and local rates.
- Site Preparation: Costs for site prep, including foundation work, can vary.
- Permits and Zoning: Local regulations may require permits, impacting the budget.
- Additional Loads: Engineering for snow load, wind speed, and seismic zones increases costs.
Calculation of Total Price
Example Pricing Table:
Item | Cost Range |
Prefab Metal Building Kit | $7,000-$14,000 |
Foundation | $1,000-$4,000 |
Construction and Labor | $5,000-$10,000 |
Accessories and Customization | $500-$3,000 |
Delivery | $500-$2,500 |
Permits and Zoning | $100-$2,000 |
Price Comparison
When comparing prices for different types of metal buildings:
- Garages and sheds often cost less than warehouses due to their size and simplicity.
- Pole barns and C-channel buildings might offer more economical solutions.
- Quonset huts are generally cheaper due to their standardized design.
- Residential homes and workshops require more customization, which increases costs.
Design and Customization
Choosing a Building Design
When selecting a building design, consider factors such as the building style and roof pitch. Building kits often come in standard designs, which include classic, contemporary, and modern styles, yet the options for customization are broad. For example:
- Building Style: A traditional gable style with a standard roof pitch might cost less than a more complex, high-pitched gambrel design.
- Roof Pitch: Adjusting the roof pitch can affect both aesthetic appeal and practical functions, like water runoff and snow load capacity.
Customization Features
- Doors & Windows: Additional doors or windows, or opting for larger sizes and premium materials, can alter costs.
Insulation: Insulation is essential for energy efficiency and comfort, particularly in climates with extreme temperatures. The type and thickness of insulation will play a role in the pricing.- Interior Finishing: Whether you’re adding basic wall paneling or going for complete interior finishing, including drywall, trim, and flooring, each layer will contribute to the final cost.
Note: Full interior finishing might include electrical and plumbing installations, which require professional services and thus increase expenses. - Exterior Finishing: Different siding options, like basic corrugated metal or upgraded vinyl siding, affect both look and price.
Trim Package: Adding a trim package can enhance the building’s appearance and provide a finished look, resulting in a slightly higher cost.
Site Development and Construction
Site Preparation and Legalities
Proper site preparation is foundational to the construction process. This involves clearing the land, leveling the ground, and laying a suitable foundation that can support the weight and specifications of a 12×24 metal building. Costs can vary significantly based on the condition of the site and the type of foundation required—whether a simple gravel base, a concrete slab, or more complex pier and beam systems.
Legalities include securing the necessary permits and ensuring that all work complies with municipal zoning and local building codes. Permit costs can range from a few hundred dollars to over a thousand, depending on the locality.
Construction Process
The assembly and installation of the metal building are tasks that require skilled labor. The construction cost will depend on the complexity of the building design and the prevailing labor rates. While a basic 12×24 metal building may only require a few days of construction, more complex, customizable structures with additional elements like attractive facades, secure doors, or specific architectural requirements take longer and cost more.
Construction often offers the option of a turnkey project, where a single entity is responsible for all aspects of building from start to finish, simplifying the process for the owner.
Finishing Touches
Upon completion of the structure, adding finishing touches involves the installation of drywall, lights, accessories, and any additional upgrades that transform the building from a functional space to one that meets the owner’s specific needs. These upgrades contribute to the overall attractiveness and functionality of the building.
Each element added to the interior or exterior of the building can affect both aesthetics and final construction costs.
Additional Considerations
Maintenance and Durability
Metal buildings are low maintenance and durable, making them an efficient choice for commercial and residential needs. Steel structures, with proper care, resist weathering and decay better than many traditional constructions. For instance, an I-beam or C-channel steel building requires only periodic inspections and basic cleaning to maintain its integrity over time. It should be noted that the location can influence the frequency of maintenance due to weather effects or local environmental conditions.
Choosing the Right Supplier
Selecting a reputable supplier is crucial for acquiring a high-quality metal building. A supplier’s website is a great place to start, offering detailed information on available materials and designs. Clients should look for suppliers who offer prefabricated kits, which are known for their time-saving and energy-efficient attributes. Before making a decision, one should contact the supplier directly, either through a call or website contact form, to ensure they understand the specific needs, such as living quarters, man cave, storage building, or agricultural purposes.
Potential for Expansion
A metal building’s versatility allows for easy modification or expansion to accommodate growing business operations or lifestyle changes. Planning for expansion during the initial design phase can save time and money in the long run. This may involve selecting a modular design that can grow with your commercial or personal needs. By anticipating future needs, clients ensure that their metal building remains functional and adaptable.