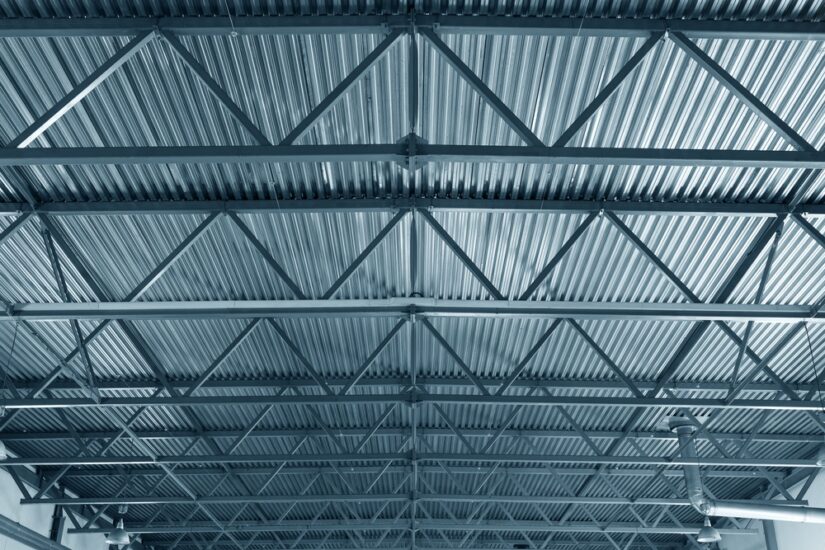
A 30 x 50 metal building offers a versatile and durable space that suits a variety of needs, from commercial warehouses to personal workshops. Typically, these structures provide 1,500 square feet of uninterrupted space, making them ideal for storage, agriculture, or manufacturing purposes. The cost of a 30 x 50 metal building can vary significantly based on several factors, including the quality of materials, the complexity of the design, and regional price differences for labor and materials.
The base price for a standard 30 x 50 metal building kit might range from $10,000 to $20,000, but this is only a starting point. Upgrades such as insulation, additional doors, windows, and various roof styles can increase the total cost. Prices will also reflect the current market rates for steel, which fluctuate due to global supply and demand. It’s crucial to consider the complete scope of the project, including foundation work, assembly, and any necessary permits when calculating the total investment required.
Fundamentals of 30 x 50 Metal Buildings
Understanding the Basics
A 30 x 50 metal building typically refers to a structure that is 30 feet wide by 50 feet long, providing a total of 1,500 square feet of space. These steel buildings are known for their durability and strength, which is imparted by the metal’s natural properties. Most metal buildings, including this size, come in prefabricated kits, which include all components necessary for assembly.
Types of Metal Buildings
Metal buildings that measure 30 x 50 can be categorized into different types:
- Standard: Rectangular structures, often used for storage or as a metal garage.
- Custom: Includes variations with added features like windows, insulation, and custom doors.
- Combination: Part workshop or commercial space, and part storage area; ideal for businesses.
Each type may be constructed using different metal building kits, which provide all necessary components such as beams, frames, and sheet metal. Advancements in steel building design allow for quick assembly and long-term reliability, making them a popular choice for personal and commercial applications.
Cost Factors for 30 x 50 Metal Buildings
Material and Labor Costs
Materials constitute a substantial portion of the overall cost. For a 30 x 50 metal building, framing and sheeting are primary components, with prices fluctuating based on the metal quality and market rates. Insulation is another cost variable, as it enhances energy efficiency and requires specific materials and additional labor. Labor costs can vary widely depending on regional wages and the project’s complexity.
- Framing and Sheeting: Cost influenced by steel market prices.
- Insulation: Types and thickness affect price.
- Labor: Skilled labor necessary for proper installation.
Customization and Additional Features
Custom features such as doors, windows, and specialized paint options can push costs higher. A standard 30 x 50 metal building comes at a base price, but additions or customizations, like a customized building system, are additional investments.
- Doors/Windows: Prices rise with size and quality.
- Customized Paint: Specialty coatings incur added costs.
- Customization Options: Architectural features increase complexity and price.
Geographical Impact on Pricing
The location where a metal building is erected influences costs in several ways. Climate demands may necessitate upgraded insulation or specific sheeting material for weather resistance. Additionally, local building codes can affect the framing requirements. Transportation costs for materials and accessibility of labor also play a direct role, sometimes offering cost savings if the building site is near suppliers or manufacturing facilities.
Installation and Construction
DIY Building Kit vs. Professional Installation
A DIY building kit typically includes all the necessary components for the owner to undertake construction, which can lead to significant savings on labor costs. However, this requires a certain level of skill and an understanding of construction practices. In contrast, professional installation by a licensed contractor ensures that the building is erected efficiently and complies with local building codes. Enlisting professionals may add to the overall cost but guarantees expertise and often comes with warranties.
- Costs:
- DIY Kit: Typically ranges from $5,000 to $15,000.
- Professional Installation: Adds $3 to $10 per square foot.
Foundation and Ancillaries
The foundation is crucial for the structural integrity of a metal building. A concrete slab is the most common foundation for these buildings, with costs averaging $4 to $8 per square foot. This price can vary based on geographical location and complexity of the site. Additional construction elements such as gutters and downspouts are essential for effective water drainage and can prevent damage. Electrical wiring and plumbing installations are intricate processes that often require professional expertise to ensure compliance and safety.
- Foundation: A concrete foundation can range from $6,000 to $12,000 for a 30 x 50-foot area.
- Gutters and Downspouts: Approximately $3 to $5 per foot.
- Electrical and Plumbing: Varies widely based on the complexity; it’s often quoted by the job or at an hourly rate of $50 to $100 for electricians and $45 to $150 for plumbers.
Benefits and Longevity of Metal Buildings
Durability and Maintenance
Metal buildings are recognized for their exceptional durability. They can withstand harsh weather conditions, including heavy snow, high winds, and seismic activities. The use of steel provides significant resistance to decay, pests, and fire, which translates into a longer lifespan for the structure. These buildings typically require less upkeep than traditional construction materials, making them maintenance-free in some cases.
Warranty and Manufacturer Support
Reputable manufacturers usually back their metal buildings with substantial warranties. These warranties can cover anything from the primary structure to roofing and paint systems, often ranging from 20 to 50 years. Manufacturer support is also a pivotal aspect, ensuring that any issues can be promptly resolved. This support often includes access to customizable options for the buildings, catering to specific needs, which reaffirms their commitment to customer satisfaction and quality assurance.
Cost Efficiency and Environmental Impact
Metal buildings are popular for their cost-efficiency; they are more affordable to construct compared to traditional buildings due to reduced labor costs and shorter construction times. The components are often pre-engineered and fabricated off-site, leading to greater precision and reduced waste. Moreover, the materials used are frequently recyclable, which reduces the environmental impact. The energy efficiency of metal buildings can be enhanced with additional insulation, making them versatile in meeting various environmental standards and reducing operation costs.
When it comes to investing in a steel building, we all seek perfection, and that’s precisely what you’ll receive when you purchase from US Patriot Steel.